To maintain fair competition and preserve the integrity of competing manufacturers, Heron Innovators, Inc. may redact or anonymize specific references to them in this text. Our aim is to provide objective and informative content without influencing their reputation. If you have any concerns or questions, please contact us. Heron Innovators is committed to upholding ethical standards and unbiased reporting.
A New Pretreatment Technology
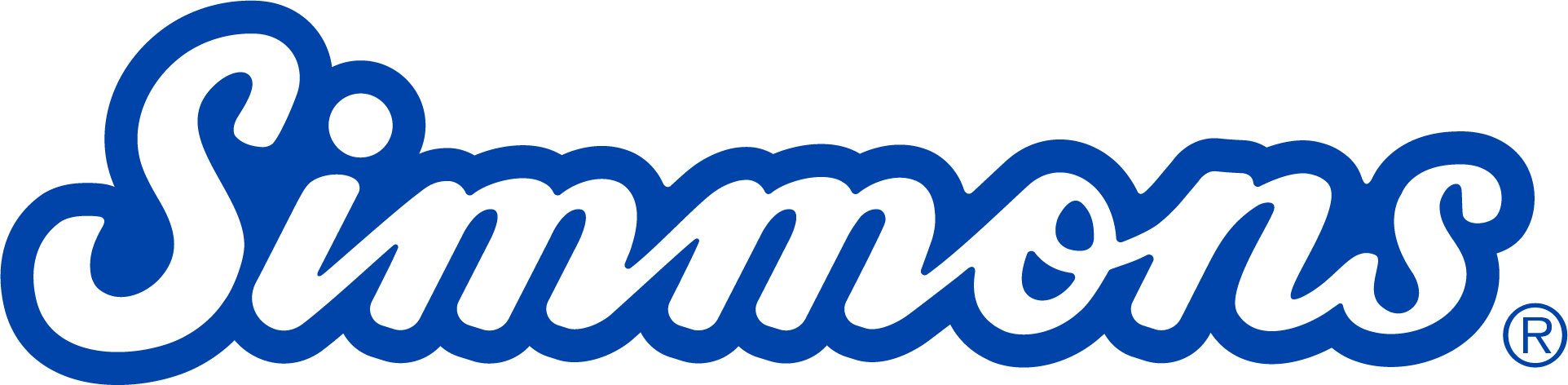
A New Pretreatment Technology Case Study:
Suspended Air® Flotation
Simmons Foods in Siloam Springs, Arkansas
Andy Brashear, Area Environmental Manager, Simmons Foods
- SAF® = Suspended Air® Floatation
- Uses froth made from an anionic surfactant, water, and air instead of
air bubbles for flotation. - One gallon of froth = 0.8 ml soap =
- 0.6 gal water and 0.4 gal (0.05ft3) air.
- Bubbles have an anionic charge so are attracted to the floc.
- Increases flotation rate so units can float 20-40 lbs (spec’ed at 30lbs)
of solids per square foot per hour (lbs/hr/ft2). - Decreases the size of the unit vs. DAF; no lamella style plates
- Less Maintenance
- More Highly Dewatered Skimmed Solids
- Better Results – Water Clarity
What is SAF®?
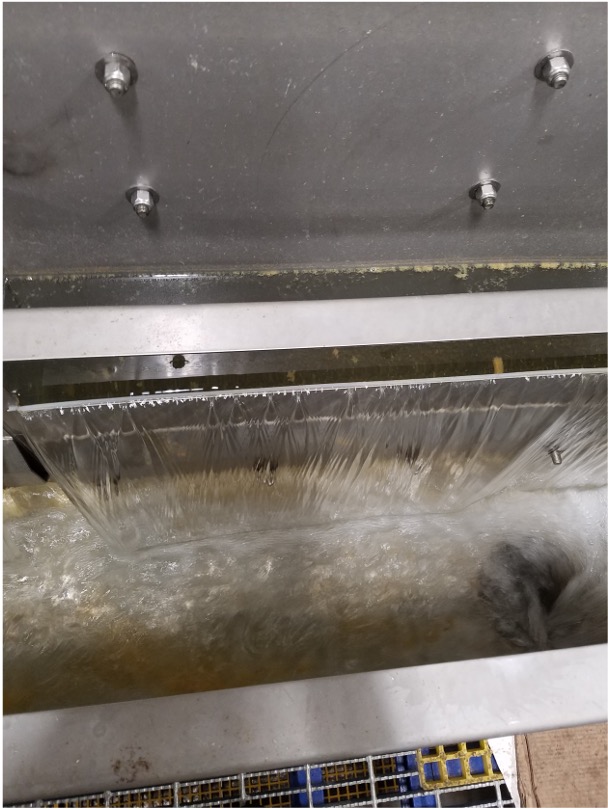
- Installed two new units in Siloam Springs*One primary
- One Secondary
- Installed one new unit in Van Buren
- Primary treatment.
- Converted two existing DAF units to SAFs in Southwest City.
- One primary
- One Secondary
Simmons has gone SAF®
New SAF® Units for Siloam Springs.
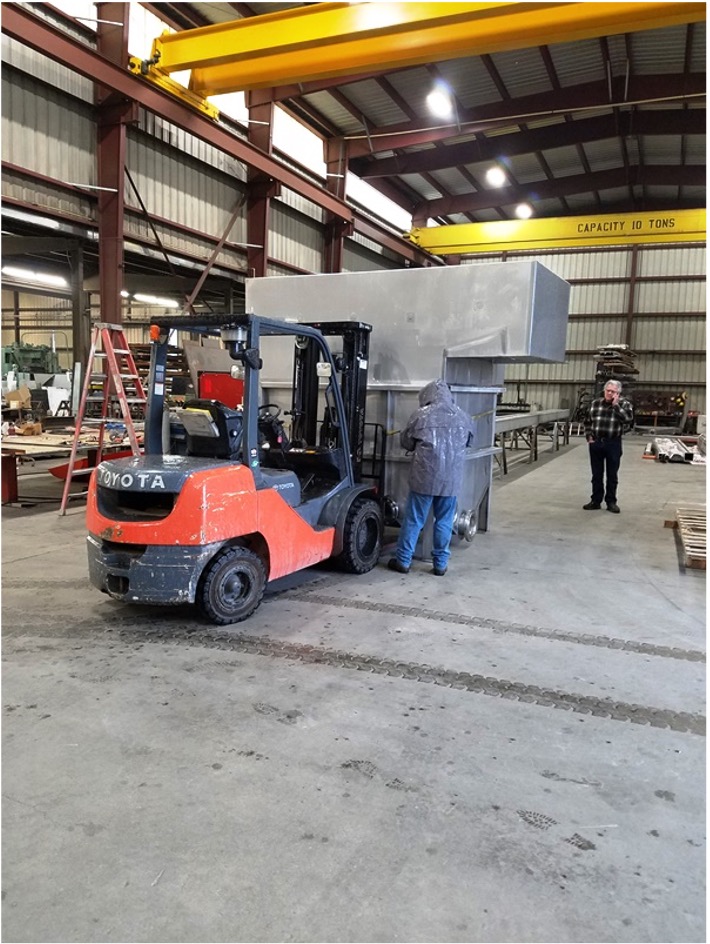
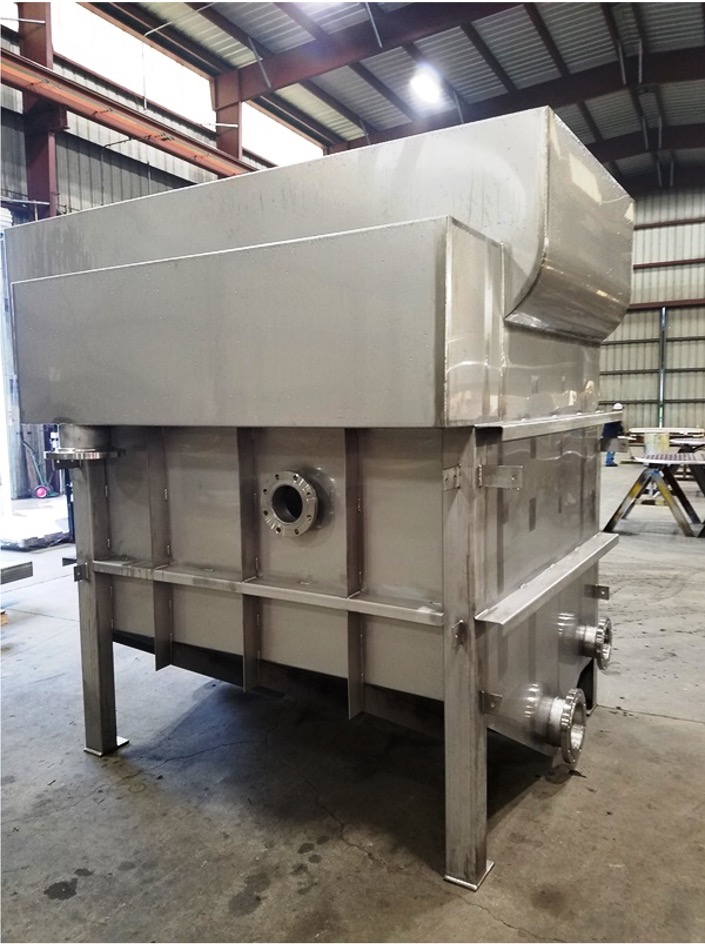
Siloam Springs SAF® Effluent
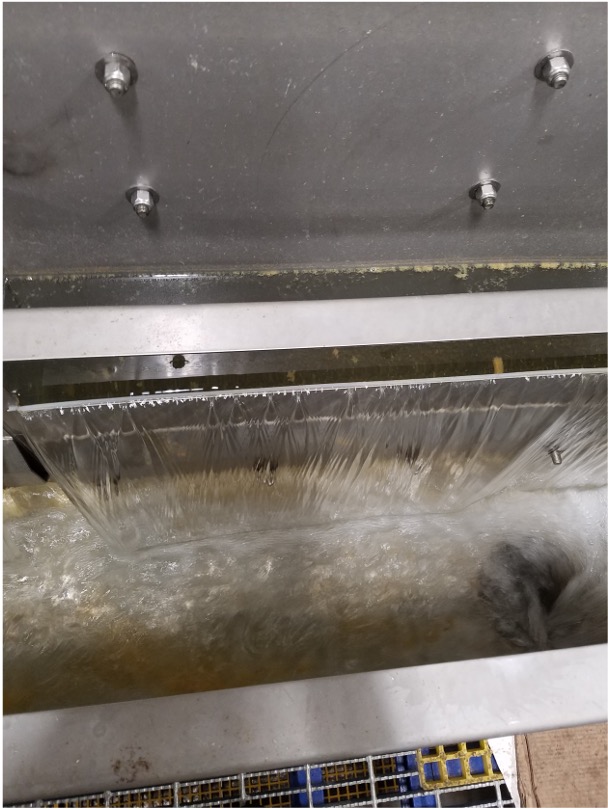
- ClearFloater Model CF250
- 35ft2 Float Cell – rated for 700 gpm @ 3000Mg/L TSS
- 350 gpm – current actual flow
- From Secondary SAF
- Influent flow contained 3000 mg/L MLSS.
Froth Generator
Model F-200 Froth Generator Shown
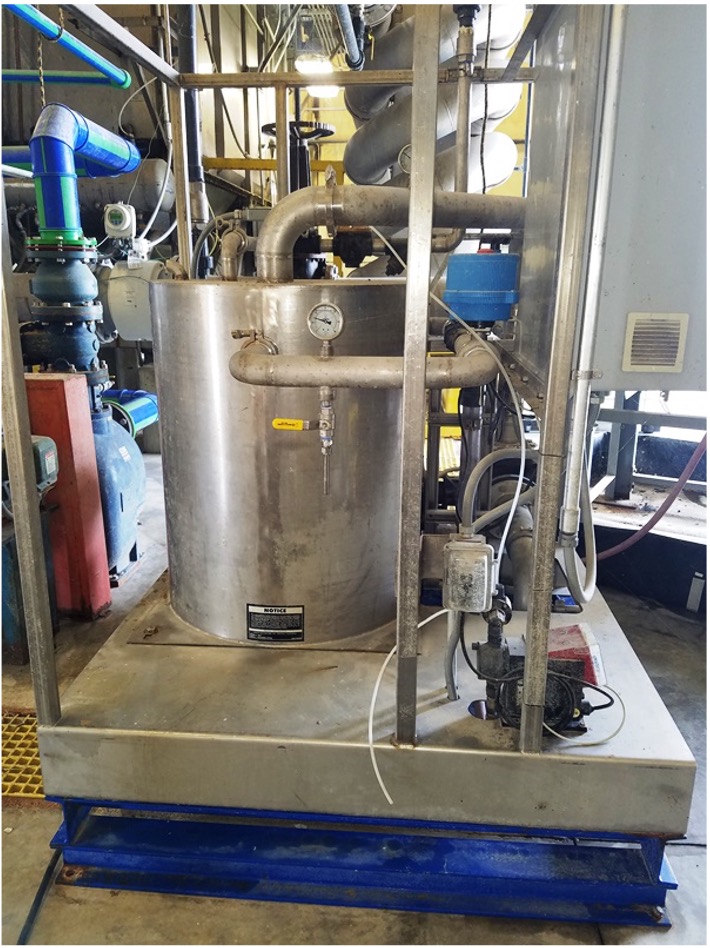
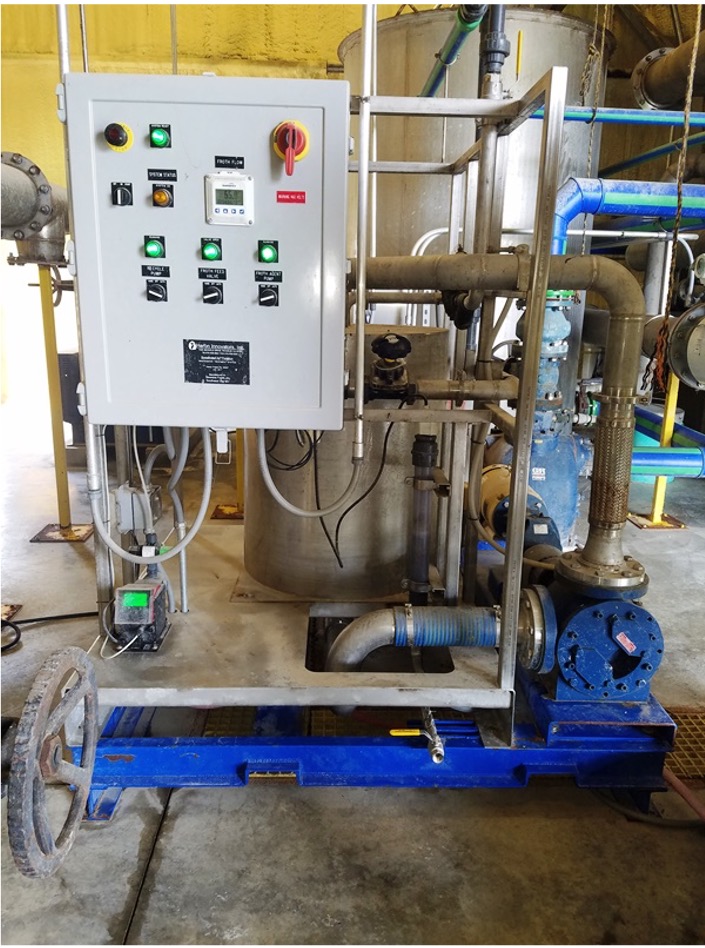
Froth Flow Meter & Froth
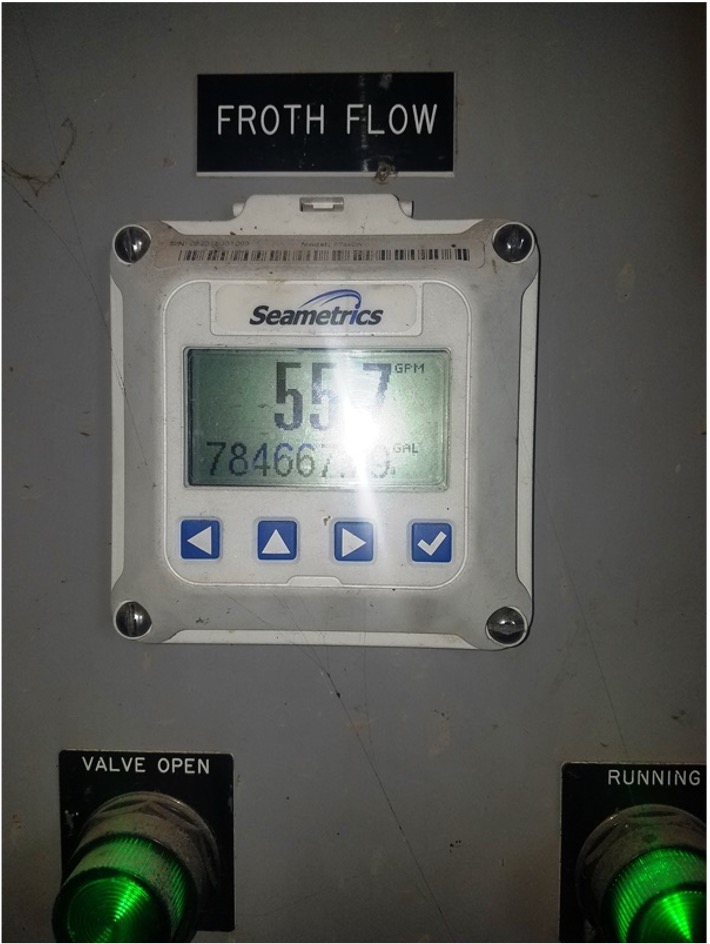
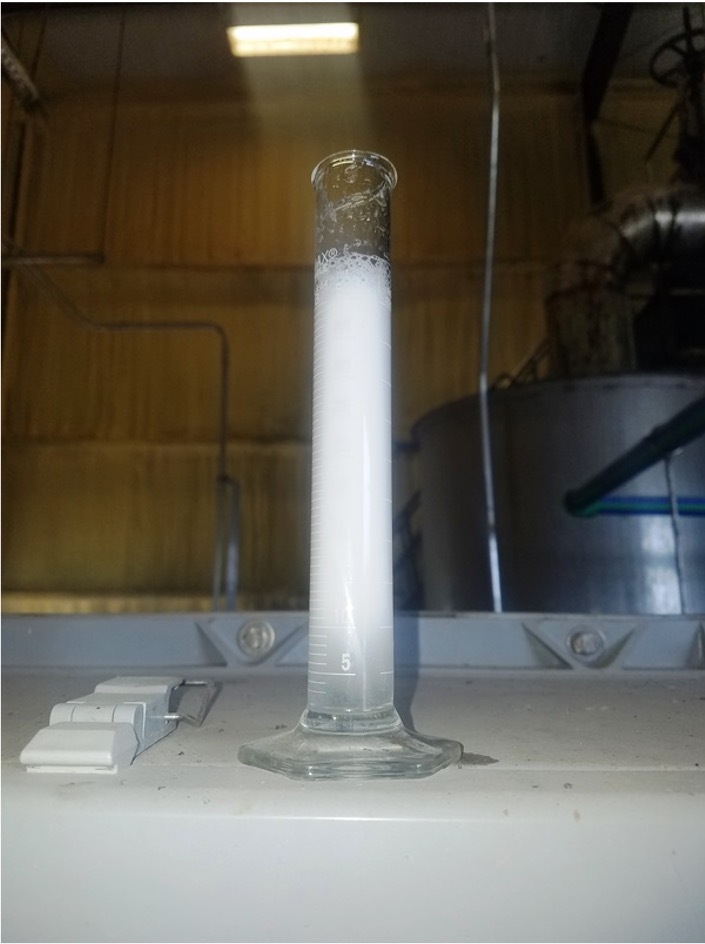
Froth Generation Summary
- Tote of Anionic Surfactant.
- Froth Generator.
- Surfactant metering pump.
- Water line.
- Froth pump.
- Holding tank.
- Flow meter.
- Flow control valve.
- Floc Mixer – Active Mixing Chamber.
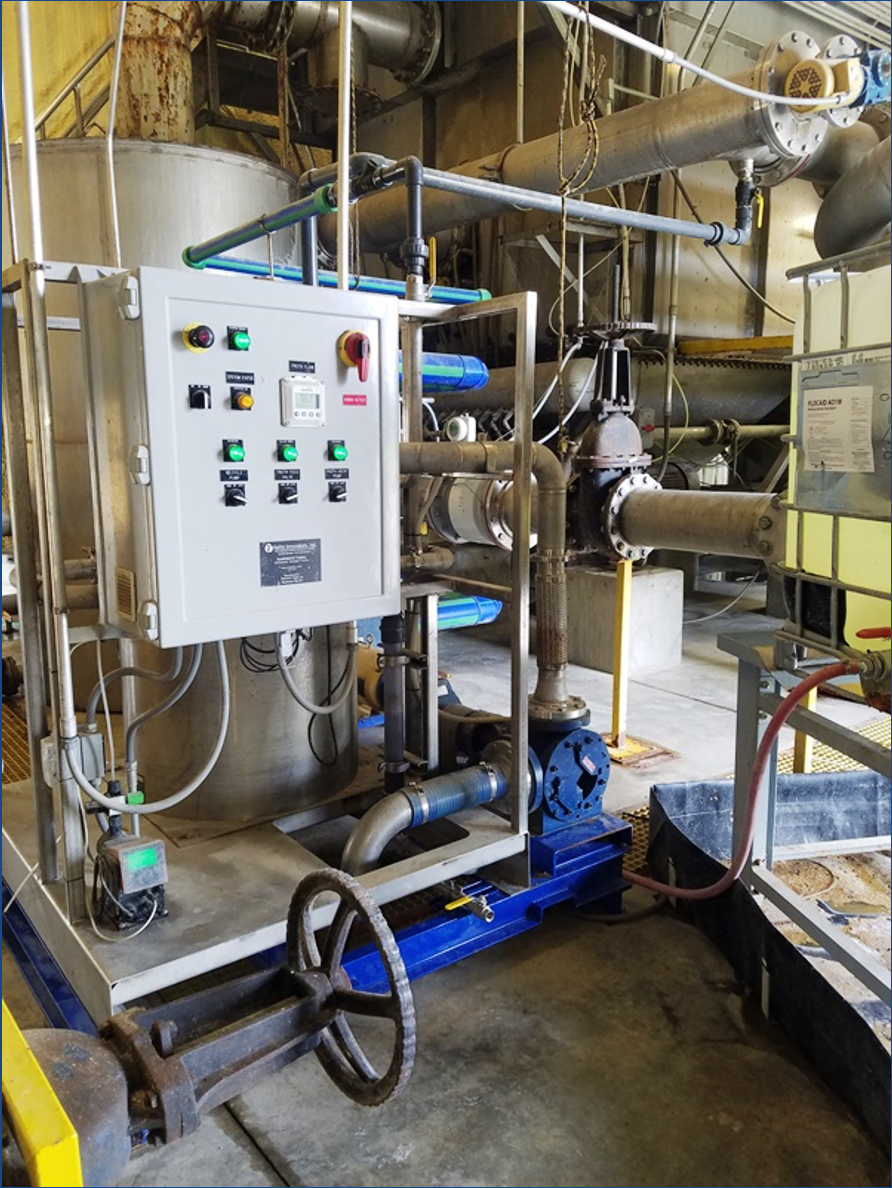
DAF to SAF Conversion:
Froth Generator & Floc Mixer
Floc Mixer – replaces previous connection from floc tube to DAF inlet flange
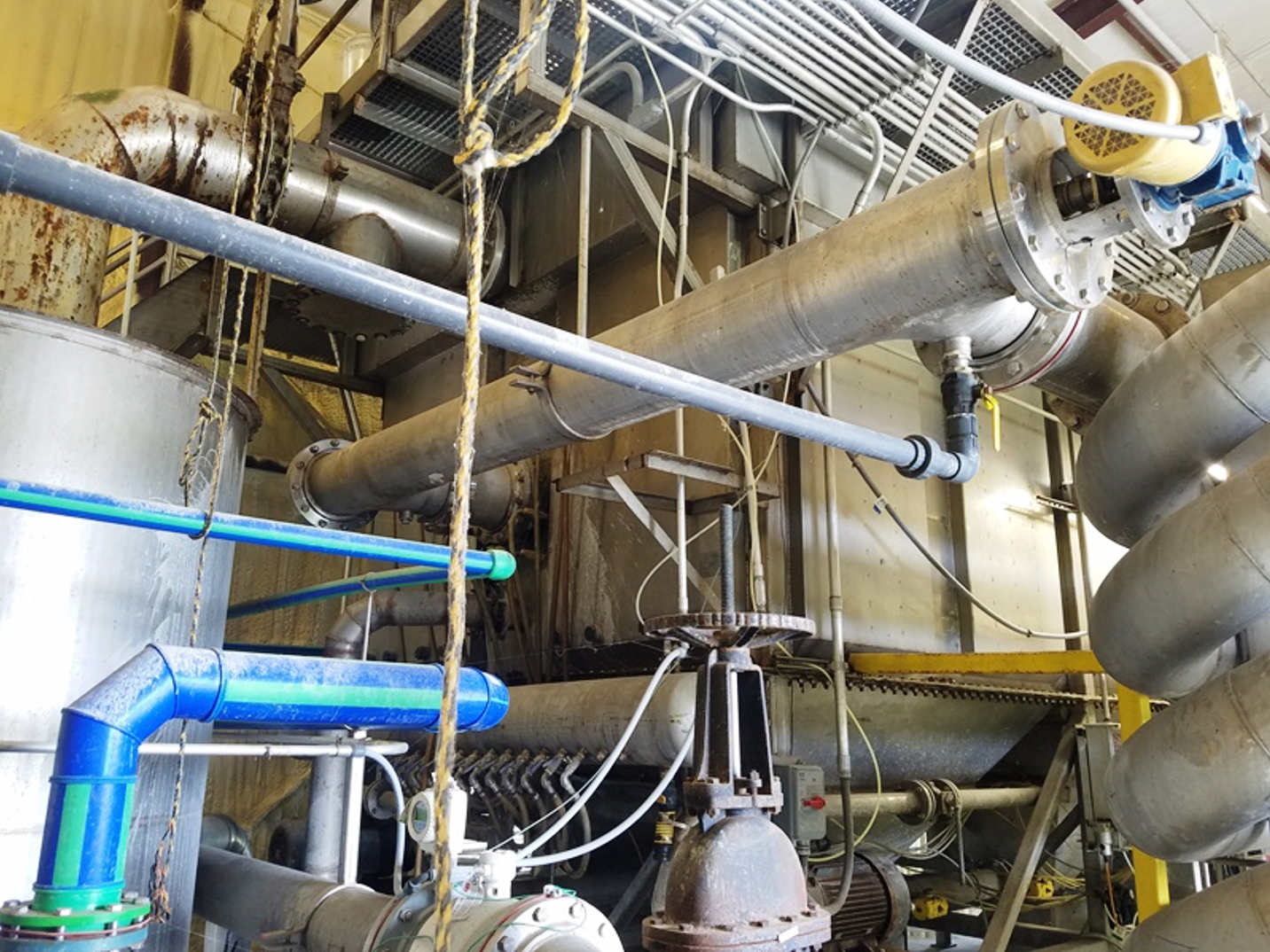
Secondary SAF®
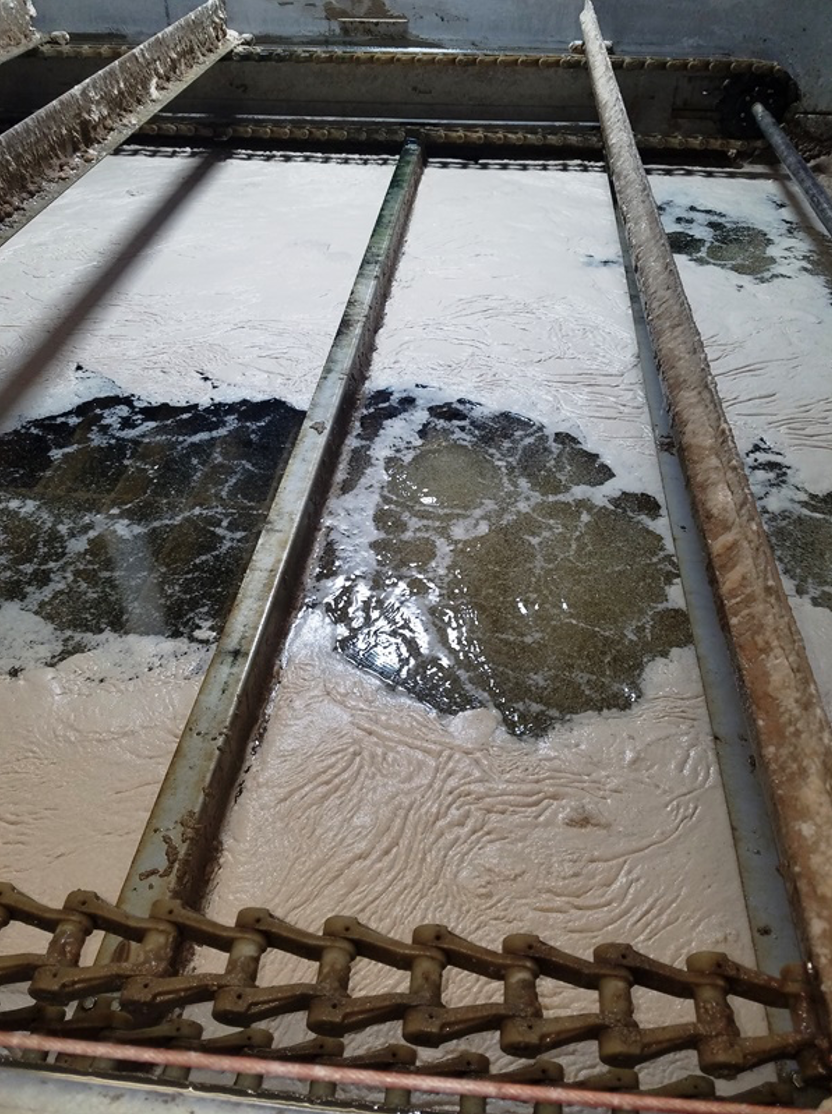
-
Secondary DAF
-
216 ft2 of surface area.
-
At 1.8 MGD before SAF conversion it could handle 1500 mg/L influent suspended solids.
-
It now handles 3500 mg/L with no carry over Average effluent TSS = 15 mg/L.
-
Specified Maximum Flow @ Current Loading ~3500 gpm
Secondary SAF® Effluent
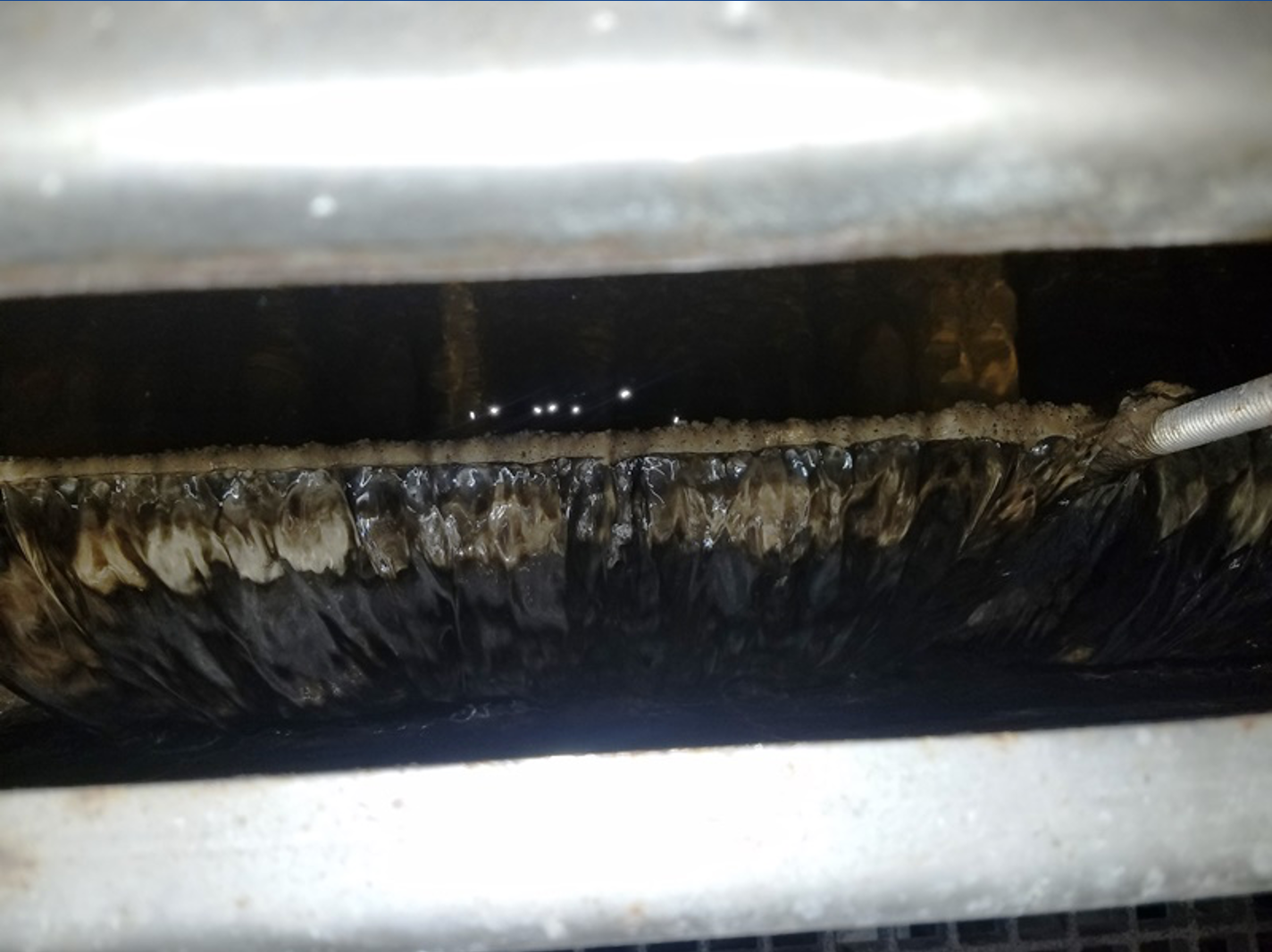
Secondary DAF to SAF® Cost Comparison
Secondary DAF |
60 HP Recirculation Pump $31,367/yr @ $0.08/KWHR |
N/A |
Coagulant Consumption: $350,000/yr |
Cationic Polymer Consumption: 120Lbs/Day; $87,600/yr |
Total O&M Costs/yr: $468,967 |
SAF® Conversion |
Equivalent – 10HP; $5,230/yr @ $0.08/KWHR |
Frothing Agent Consumption @ 25 GPM Output; (1)-tote/6wks; $38,780/yr |
Coagulant Consumption: $140,000 |
Cationic Polymer Consumption: 60Lbs/Day; $43,800/yr |
Total O&M Costs/yr: $227,810 |
Net Savings/yr: $241,157 |
*Difficult to quantify savings associated with directly reclaiming water vs requiring additional treatment
Primary DAF to SAF® Conversion
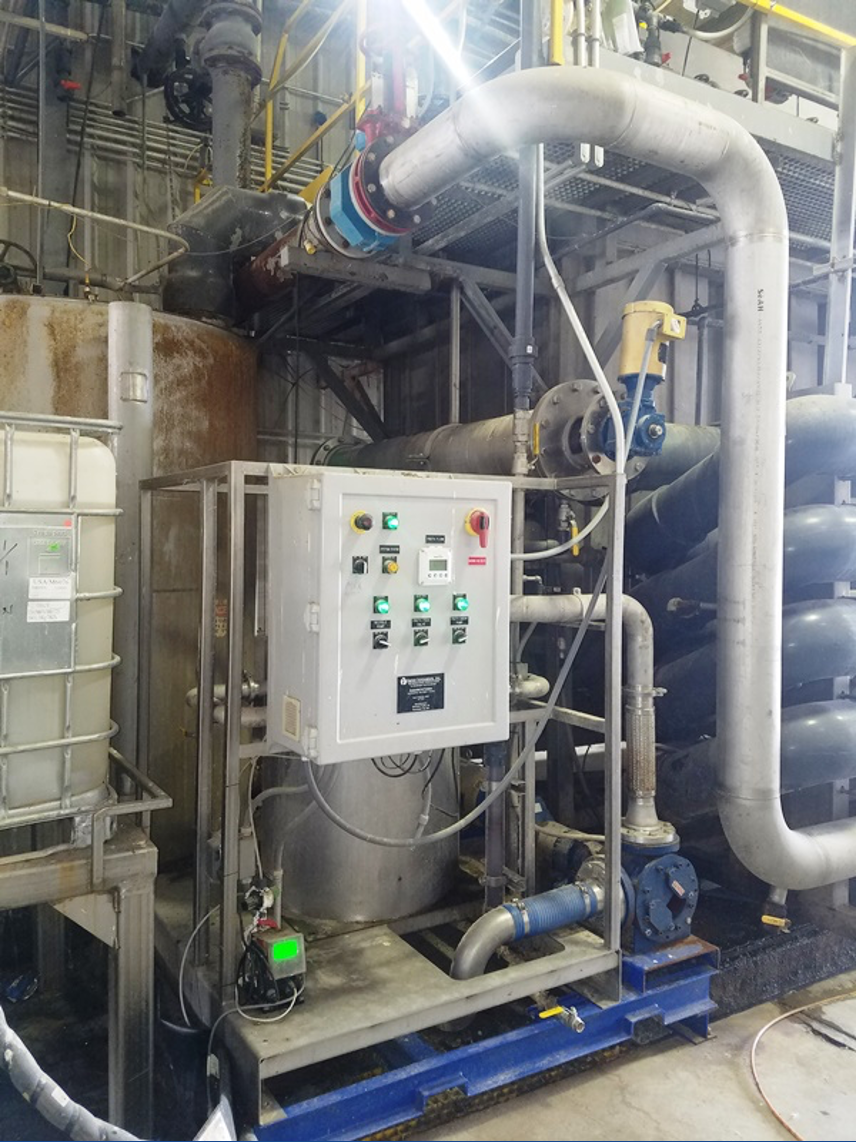
-
Converted Primary DAF.
-
It was maxed out at 1250 gpm and 2000 – 2500 mg/L influent solids.
-
It now treats an additional 700 gpm.
-
Specified to treat a maximum 2400 gpm.
-
Cost effective way to increase capacity.
Primary DAF to SAF® Cost Comparison
Primary DAF |
40 HP Recirculation Pump $20,920/yr @ $0.08/KWHR |
N/A |
Organic Coagulant Consumption: 700Lbs/Day; $130,000/yr |
Cationic Polymer Consumption: 120Lbs/Day; $87,600/yr |
Anionic Polymer Consumption: 110Lbs/Day; $50,000/yr |
Total O&M Costs/yr: $288,540 |
SAF® Conversion |
Equivalent – 10HP; $5,230/yr @ $0.08/KWHR |
Frothing Agent Consumption @ 25 GPM Output; (1)-tote/6wks; $38,780/yr |
Organic Coagulant Consumption: 350Lbs/Day; $65,000/yr |
Cationic Polymer Consumption: 120Lbs/Day; $87,600/yr |
Anionic Polymer Consumption: 0-Lbs/Day; $0.00/yr |
Total O&M Costs/yr: $196,610 |
Net Savings/yr: $91,930 |
Conclusions
-
SAF is mechanically simpler than a DAF:
-
Removes recirculation pump, header, compressor, and air lines.
(No more air lines plugging in header which would also cause packing to blow out on recirc pump.) -
No requirement for lamella style plates
-
Less maintenance
-
It’s operator friendly.
-
It’s 6 times more efficient than a DAF (20-40 lbs/hr/ft2 vs. 5 lbs/hr/ft2).
-
You can adjust the froth flow (i.e. floatation air) to the loading.
-
Feed less chemical (less polymer mixing).
-
Better results
-
Thicker Solids
Download The Full Presentation
Fill out the form to download the full presentation as presented by Simmons.