Applying Aphron Technology
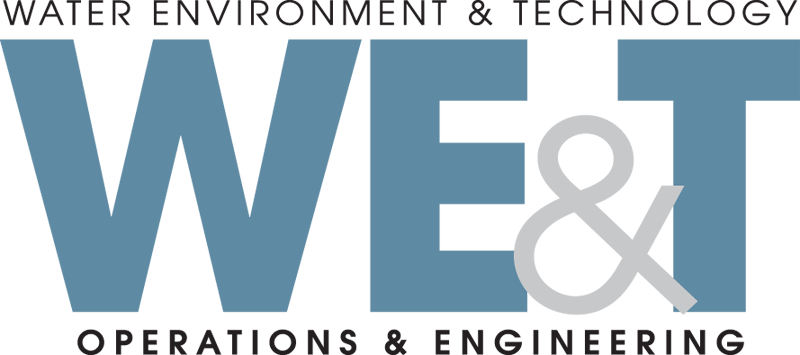
WE&T | JUNE 2022
Innovation in air flotation leads to solid alternative to a legacy process
George Tchobanoglous, Harold Leverenz, and Dan Zeller
The total solids content of waste activated sludge (WAS) varies considerably, depending on the operation of biological reactors and clarifiers. Thickening is a procedure used to increase the solids content of WAS by removing a portion of the liquid fraction. To illustrate, if waste activated sludge, which is typically pumped from secondary settling tanks with a content of 0.4% to 0.8% solids, can be thickened to a content of 4% solids, then a fivefold decrease in sludge volume and corresponding increase in digester retention time is achieved.
The focus of this paper is on the performance of a relatively new process known as Suspended Air® flotation (SAF®), employing aphron-based technology for the thickening of WAS. Aphrons are used because they are resistant to coalescence, as shown on Figure 1, and their chemistry can be tuned to adsorb constituents based on surface charge. In addition to achieving high WAS solids separation efficiency, based on onsite testing, the principal advantages of the SAF® process include relatively small process footprint, low power requirement, low chemical usage, and the ability to handle high concentrations of suspended solids (up to 16,000 mg/L in this study).
Based on the results from a Kansas facility, the SAF® process is an attractive alternative to the legacy dissolved air flotation (DAF) process. Because of the effectiveness of the SAF® process, as described in this paper and in other studies, it is anticipated that it will find broader applications in the field of wastewater management.
The Process
Advances in aphron generation technology, the production of finer aphrons, and the development of process scale-up techniques have resulted in the current commercial implementation known as the SAF® process. The principal components of the SAF® process are illustrated on Figure 2. The SAF® process uses an externally generated suspension of micron-sized aphrons. They are about 7 to 25 µm. The volumetric air content of the aphron bubbles in water is typically in the range of 40% to 50%. Each of the bubbles is coated with a thin film of an electrically charged, chemically active frothing agent, such as a soap film. The film is either anionic or cationic depending on the application.
As noted previously, because the air bubbles are charged, they do not coalesce. Instead they are attracted readily to oppositely charged wastewater solids to be removed. The polymer and aphron froth are injected into the influent, upstream of a mixer, before entering the flocculation portion of the flotation tank (See “Influent (1)” on Figure 2(a)).
The flocculated solids then move to the flotation portion of the tank where they float to the surface and are removed by skimming. The clarified underflow passes under a baffle and over a weir into a launder. In some applications where the natural charge density of the solids is too low for effective flotation, a coagulant is also used. Operationally, coagulant is dosed and contacted with the solids using a pipeline flocculation reactor. The flocculated solids are then contacted with polymer and aphron froth before being released into the flocculation zone (See “Influent (2)” on Figure (2a)).
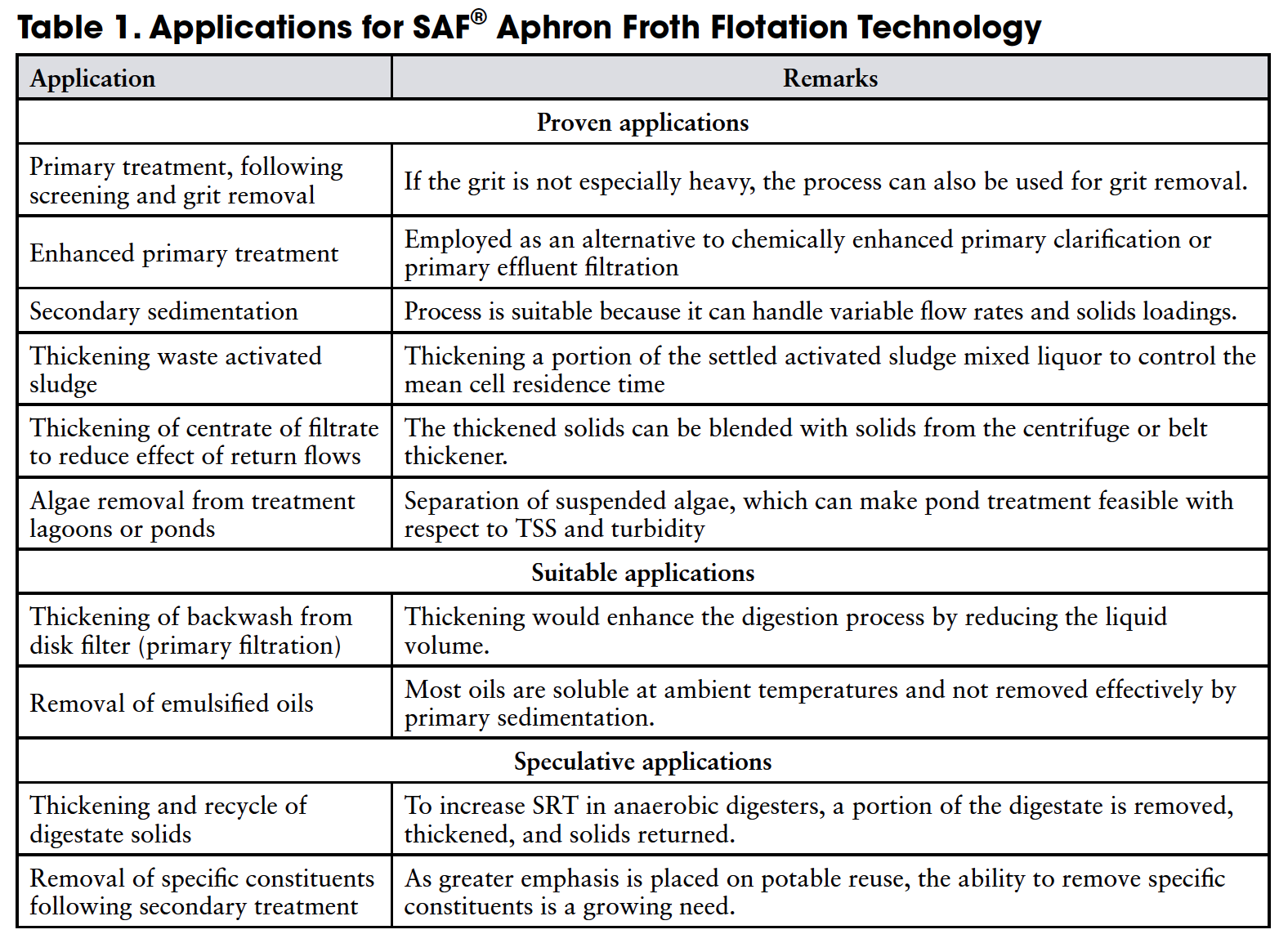
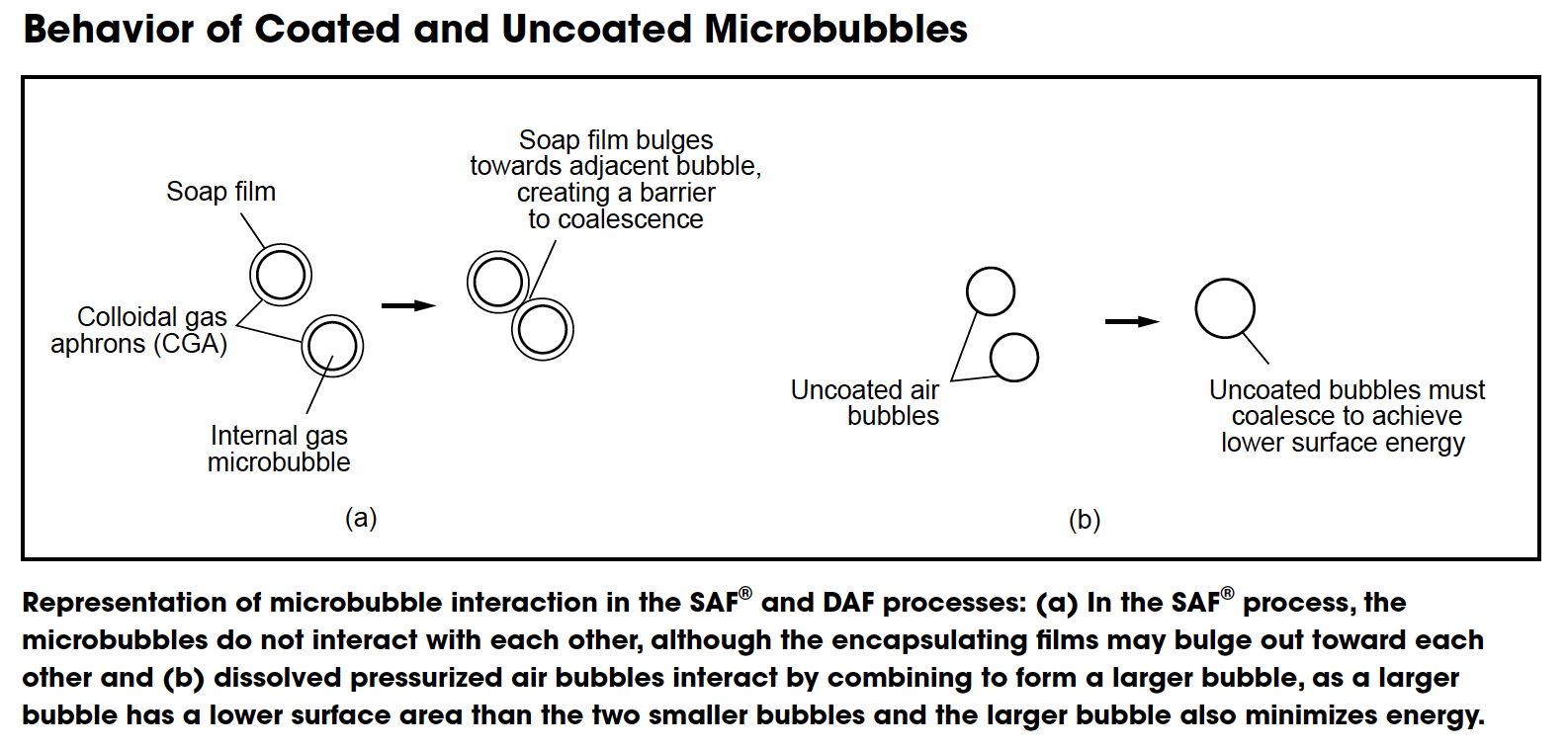
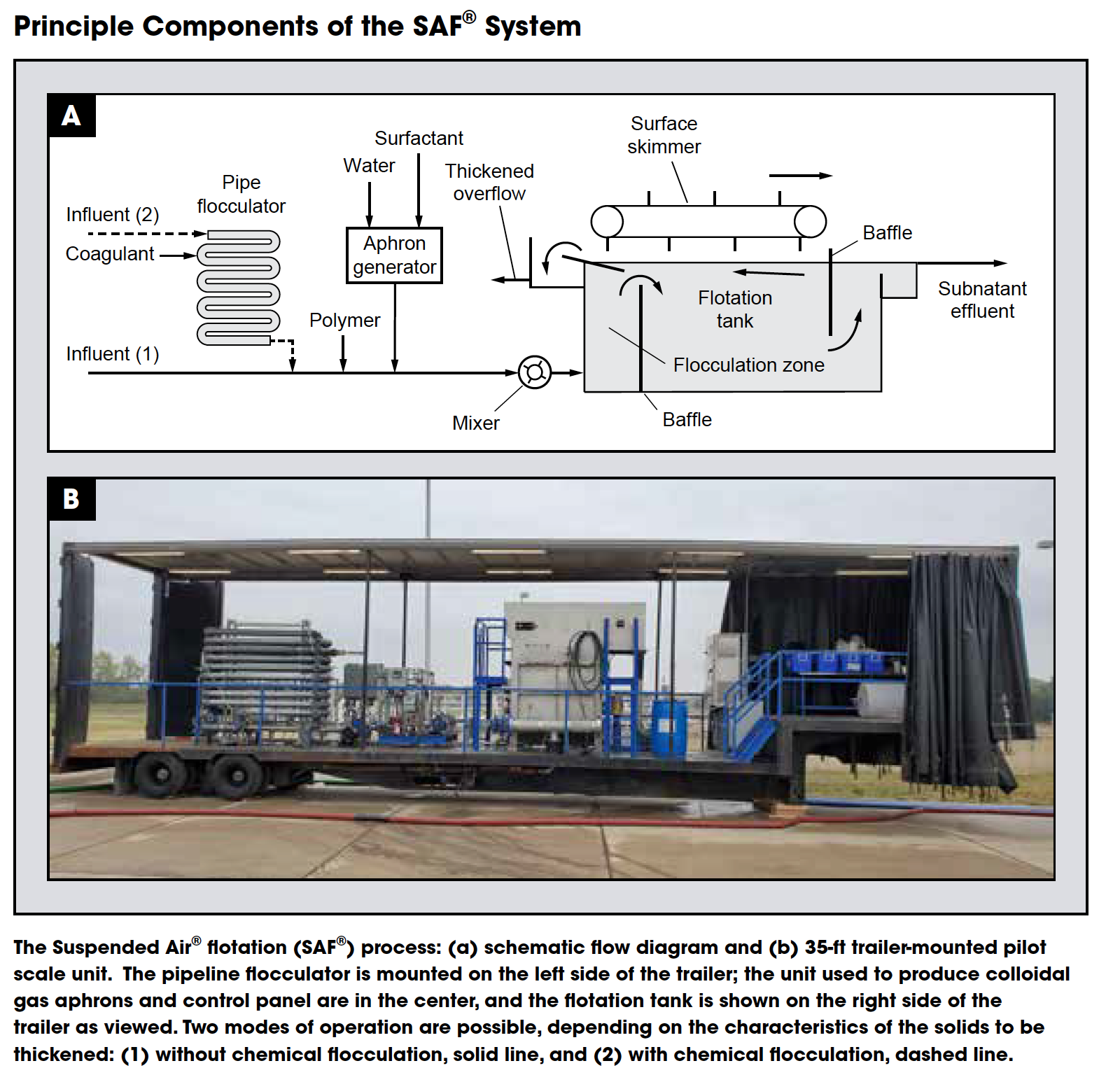
Application of SAF® Process
The SAF® process has been tested in several different wastewater treatment applications, as summarized in Table 1. A full-scale pilot test at the University of California, Davis, with screened untreated wastewater found that the SAF® process can replace three-unit processes: grit removal (except for the largest and densest particles), primary clarification, and primary scum handling. Other applications for the SAF® process are in digestate thickening (pilot tested in Austin, Minnesota; Sacramento, California), waste activated sludge thickening, the focus of this paper, and clarification of algae-laden pond water (Graton, California; Colfax, California; Pleasant Valley, California) especially as pretreatment for tertiary filtration.
Thickening WAS in Topeka, Kansas
The Oakland Wastewater Treatment Plant is one of three municipal water resource recovery facilities serving the City of Topeka, Kansas, and the surrounding area. The typical influent flowrate for the Oakland facility is 45,000 to 57,000 m3/d (12 to 15 mgd). The facility process flow diagram, rationale for piloting of the SAF® process, SAF® performance, and a discussion of the results are presented below.
Process Configuration
A process flow diagram for the Oakland facility is shown in Figure 3. As shown in the flow diagram, the DAF process, consisting of two units operating in parallel and already in service for more than 50 years, was being used to thicken WAS. At peak flow, the DAF units were able to process a combined WAS maximum flow rate of 1.9 m3/min (500 gal/min). The solids loading rate to the DAF units ranged from 0.04 to 0.08 kg/m2·h (1 to 2 lb/ft2·h). The DAF float solids, which ranged typically from 3% to 5% solids, were being pumped to two stage anaerobic digesters.
Rationale for Pilot
In late March 2020, the gearbox for the drive assembly on one of two DAF units failed resulting in a significant loss of WAS thickening capacity. Because the DAF units had exceeded their design life, there were significant costs associated with fabrication of replacement drive parts. Additionally, replacement drives would take 6 to 8 months to deliver. In response to these conditions, the facility implemented a strategy to continue meeting effluent quality requirements while addressing the limited capacity to process solids. The strategy consisted of three main steps.
First, operators diverted a portion of the influent wastewater to other treatment facilities, reducing the influent flowrate to 30,000 to 34,000 m3/d (8 to 9 mgd).
Second, they stored excess WAS within the facility. They did this by using one unused biological reactor, increasing the mixed liquor suspended solids concentration within the two operational biological reactors, and allowing the sludge blanket in the secondary clarifiers to increase to 4.7 m (15 ft) as opposed to the normal operating depth of 0.6 m (2 ft).
Third, they pilot testedof the SAF® process as an alternative thickening technology in October 2020.
Soon after the DAF drive box had been replaced, one of two thickened solids pumps seized. This again limited the WAS thickening capacity of the legacy equipment. In response, another SAF® unit was placed into service to reduce the backlog of solids.
SAF® Operational Phases
Additional SAF® operations took place from May to August and September to October 2021. In both cases, the feedstock was a blend of settled and stored WAS. The operational phase and feedstock are summarized in Table 2 (below). The facility’s normal mixed liquor suspended solids concentration varies between 2,000 and 4,000 mg/L. The corresponding settled WAS concentration, without stored WAS, is on the order of 4,000 to 8,000 mg/L, depending on the time of year and other operating constraints. The stored WAS had an age ranging from 3 to 12 months during the SAF® operation. The age of stored WAS is important because stored WAS is more challenging to dewater due to the extended decomposition of the solids, resulting in the formation of finely divided particles. These particles have proven to be difficult to remove and will generally require more chemicals for effective thickening.
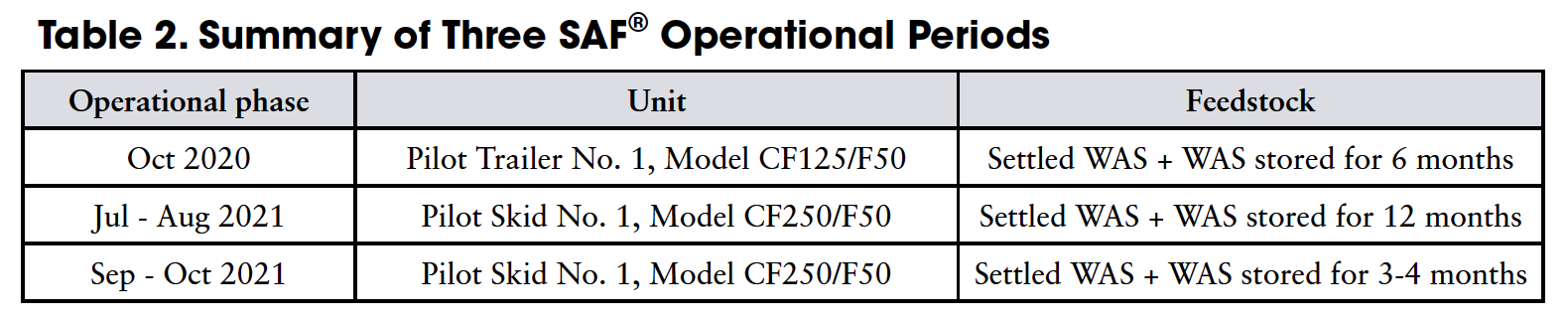
SAF® Performance
Performance data for the SAF® pilot testing with a mixture of stored WAS mixed with settled WAS are summarized in the top section of Table 3. Performance data were also collected during July and August, and then again during September and October 2021. For the entire period of operation, the removal performance was essentially the same however, the chemical usage was variable due the age and properties of the stored WAS. It is notable that the SAF® process can operate under a wide range of operational conditions, with influent TSS ranging from about 5,000 to 16,000 mg/L and process loading varying from 0.55 to 1.9 kg/m2·h (13 to 46 lb/ft2·h) for both settled and stored WAS. Typical solids loadings for the existing DAF units, when operational, were about 0.04 to 0.08 kg/m2·h (1 to 2 lb/ft2·h). The performance data summarized in the second part of Table 3 are consistent with the results obtained during typical operation. During the second period of operation, comparative energy usage was also evaluated. For the same amount of WAS processed per day, the average energy required for the SAF® was 4.9 kWh/d while corresponding energy usage for the aging DAF equipment was 49.9 kWh/d (24.9 kWh/d per DAF unit). It is anticipated that the energy usage for newer DAF units would be lower. The froth flowrate used in Table 3 is the volumetric flowrate of the aphron suspension. The froth is generated using a surfactant solution, which was being used at a rate of approximately 0.34 m3/month (90 gal/month) for processing stored WAS with an estimated age greater than 12 months. The consumption of the surfactant is set at a high level — 53 to 59 L/min (14 to 15.5 gal/min) — due to the challenging nature of processing the stored WAS.
Discussion
As shown in Table 3, the SAF® unit was able to operate at process loadings ranging typically from 0.85 to 1.7 kg/m2·h (20 to 40 lb/ft2·h), an order of magnitude higher than the existing DAF units. Additionally, the thickened solids concentration achieved using the SAF® pilot ranges from 4% to 7.5%. While providing excellent performance in solids separation and thickening, the thickened float from the SAF® process has not had any negative effect on biogas production or health of the anaerobic digestion process. Regardless of the sludge age, the typical current solids loading for the SAF® process is 1.3 kg/m2·h (30 lb/ft2·h).
From an operational perspective, the SAF® unit was found to be easy to operate under a wide range of conditions. After initial jar testing, the unit was readily put into operation at near optimum configuration. The SAF® unit continues to achieve high levels of performance with little operator attention.
The legacy DAF process was known to be difficult to adjust for ideal performance, where the effect of slight changes in the set point or influent characteristics can range from poor flotation to wasted polymer occurring as a film of polymer on the surface. In some cases, the incorrect DAF settings resulted in clogging and costly maintenance to correct. The SAF® process, by comparison, can be easily tuned by visual observation of the float color and texture. The skimmed solids have been found to be naturally self-draining of entrained water, improving the final thickened solids concentration.
With respect to polymer usage, the variable dosages reported in Table 3 are related to both the concentration and age of the stored WAS solids. It has been observed that a considerable increase in the use of polymer is needed for centrifuge dewatering those same solids after digestion. The normal polymer concentration for centrifuge dewatering of thickened WAS and primary sludge is 0.24%. To achieve the same results when dewatering primary and digested old WAS, it has been necessary to increase the polymer concentration to 0.48%.
George Tchobanoglous is a Professor Emeritus, and Harold Leverenz is a Research Engineer in the Department of Civil and Environmental Engineering at the University of California, Davis. Dan Zeller is the Operations General Manager at the City of Topeka, Kansas, Utilities Department.
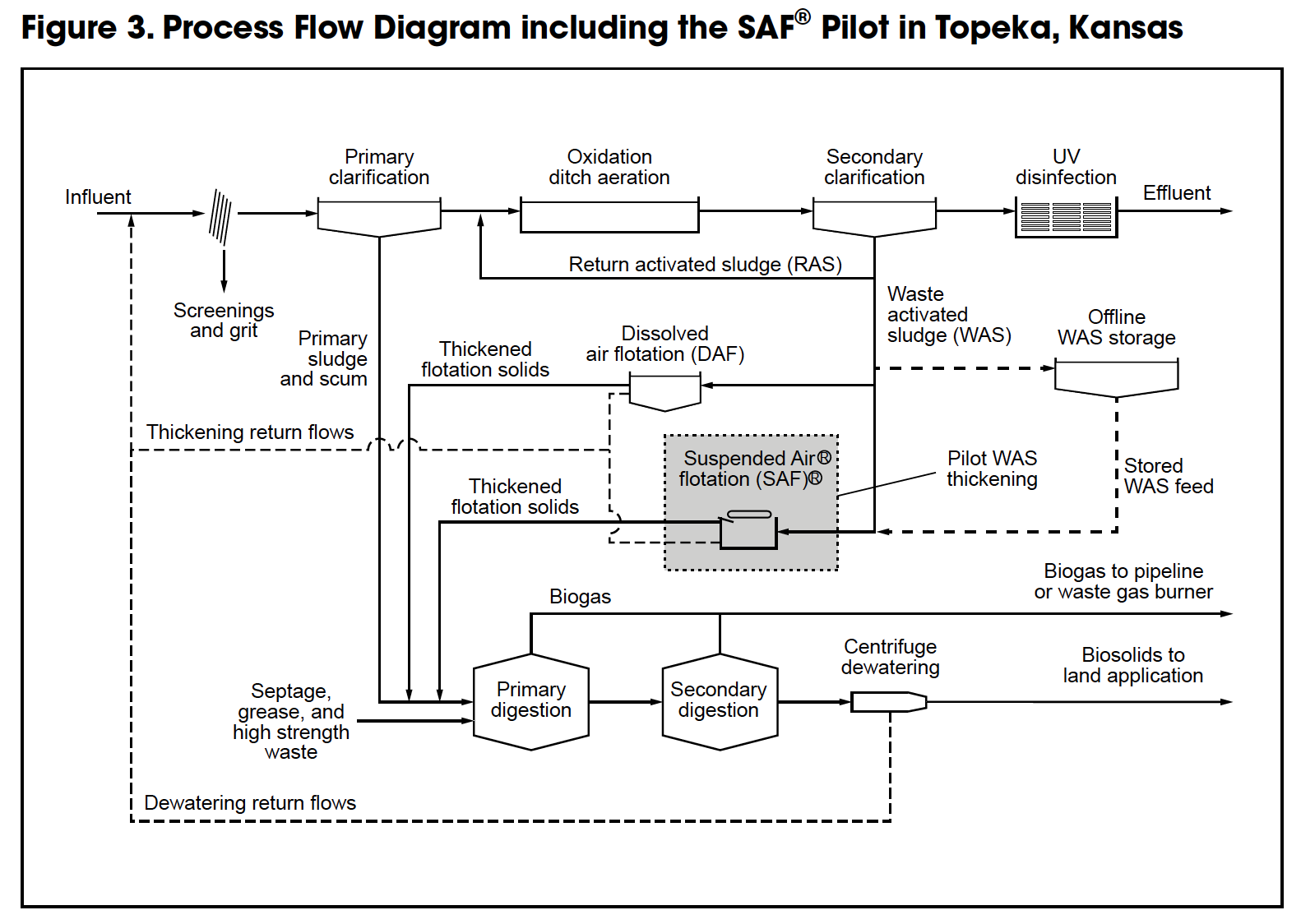
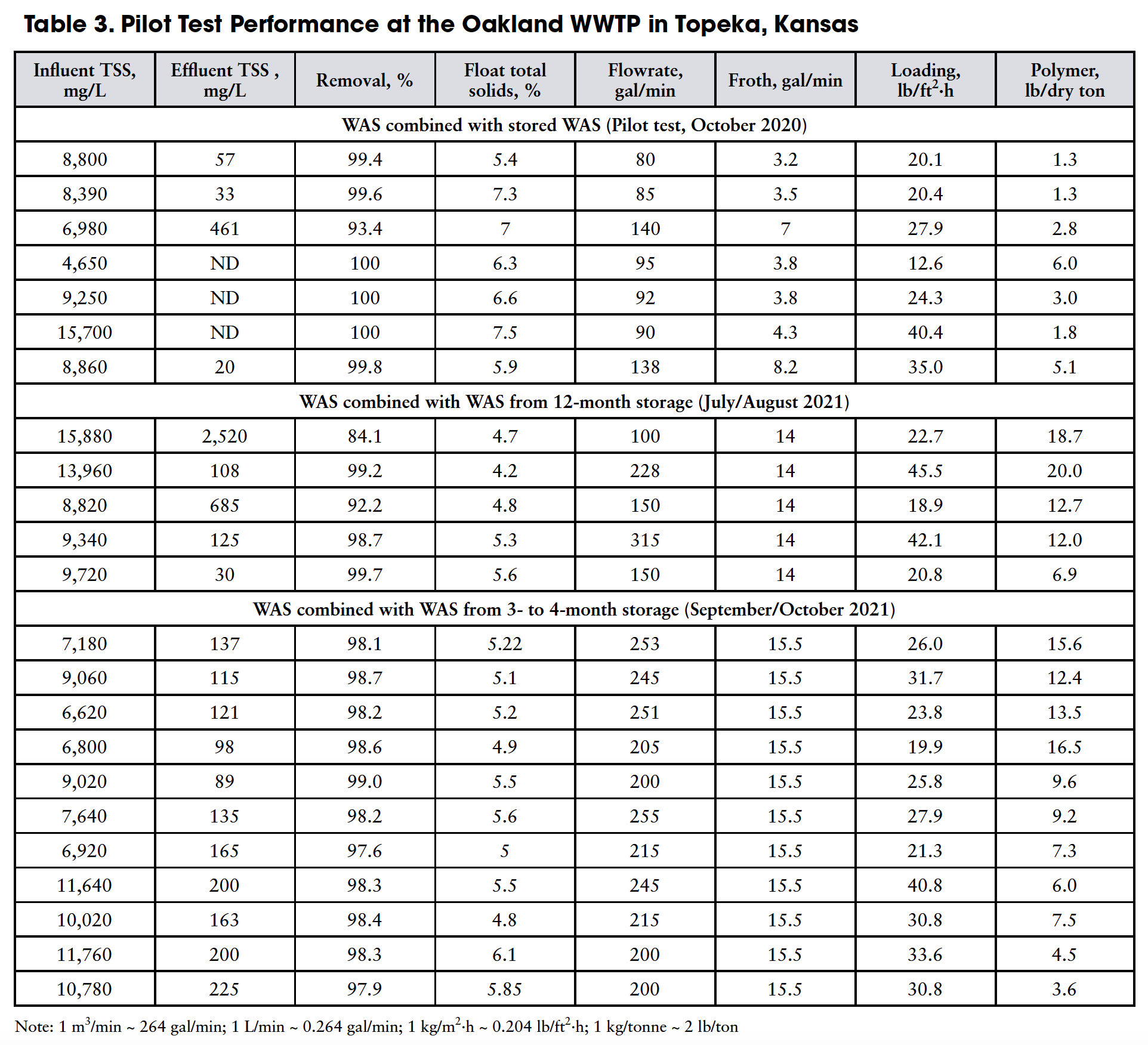
Download The WE&T Article
Fill out the form to download the full article, “Applying Aphron Technology,” as published by WE&T.