To maintain fair competition and preserve the integrity of competing manufacturers, Heron Innovators, Inc. may redact or anonymize specific references to them in this text. Our aim is to provide objective and informative content without influencing their reputation. If you have any concerns or questions, please contact us. Heron Innovators is committed to upholding ethical standards and unbiased reporting.
Austin, Minnesota | Pilot Study Results | By SEH
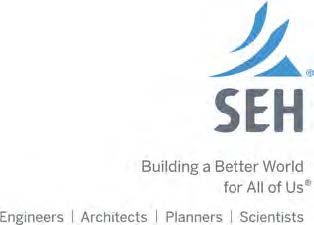
1 Introduction
The City of Austin performed a flotation separation pilot study from August 17th, 2020 – September 1st, 2020 at the Austin Wastewater Treatment Plant Site. A Dissolved Air Flotation (DAF) system was piloted at the same time as a Suspended Air Flotation (SAF) from Heron. The pilots were physically placed in the northeast corner of the Austin WWTP, between the Anaerobic Pumping Station and the Aeration Tank. Tests were collected in accordance with the schedules proposed in the Pilot Study Protocol. After the test results were obtained, they were compared between the DAF and SAF.
- The pilot study assisted in identifying:
- Efficiency gains that could be made in the treatment process
- Chemical costs associated with each particular flotation system style
- Design criteria and considerations, such as gas levels and corrosivity levels
- Expected removal efficiency of each flotation system style
- Expected waste % solids
2 Pilot Types Selected
Pilots are small scale versions of full size equipment designed to simulate a full-scale performance of the unit. The following two flotation technologies were chosen for piloting to better understand which best meets the goals for separating the industrial digester effluent at Austin: Dissolved Air Flotation (DAF) and Suspended Air Flotation (SAF). These options were selected as they were representative of two different technologies designed to float the suspended solids.
2.1 Dissolved Air Flotation (DAF)
There are many styles of a traditional DAF unit, which generally inserts compressed air into the influent stream and raises the suspended solids to the surface and then scrapes them off the top. Various technologies for inserting the air and removing the floating particles are available, and these DAFs come in many shapes and sizes. DAF units have a recycle stream that is typically
15-100% of the DAF flow.
A DAF was piloted as was thought that this technology would be representative of similar DAF technologies. The DAF company was selected for multiple reasons: (1) Hormel has a good working relationship with the company, (2) the company offered the lowest capital and 20-year life cycle costs of the several DAF proposals obtained, and (3) the manufacturer offers polypropylene material for the DAF tank, which was not offered by other manufacturers.
This company is also based out of Oklahoma and is represented locally by Great Northern Environmental.
This particular DAF included lamella plates. These lamella plates generally increase the solids loading rate which the unit can handle, which typically allows the DAF a smaller footprint than other DAF manufacturers thus decreasing cost.
2.2 Suspended Air® Flotation (SAF®)
Suspended Air Flotation (SAF) is a DAF that has modified means of inserting air into the influent stream. This technology provides the incoming air particles with an electric charge that allows for smaller than usual bubbles to insert themselves into the feed water, and remain in the water until it has brought the suspended particles to the surface. This technology is less susceptible to temperature performance variations. SAF installations are often retrofits of DAF installations to gain capacity within an existing tank volume. Pilot testing was necessary to understand the chemical demands for this alternative; of both surfactant and polymer.
The manufacturer selected for the SAF pilot is Heron Innovators (Heron), located in California. Heron has a patent on the technology and there are no other manufacturers that produce this type of unit. Heron is represented locally by Vessco.
2.3 Other Separation Technologies
In SEH memorandum dated May 7, 2020, other options were presented for the separation, which were not recommended for pilot testing, as described below:
- Dissolved Nitrogen Flotation (DNF): This is similar to the DAF technology, except utilizes nitrogen instead of air for the flotation medium. While this is a viable technology, it was not piloted because its performance and chemical use would be the same as the DA. From the DAF pilot, we would be able to assess if nitrogen would be required. Additionally, plant and Hormel staff were able to visit a DNF in Osage, IA.
- Lamella Plate Settling: Lamella Plate settling was eliminated from consideration due to the potential for plugging with fats, oils, and grease.
- Ballasted Flocculation: Deemed not viable after discussing with manufacturer.
- Membrane Bioreactors: Eliminated due to extremely high capital cost.
- Rehabilitation of Existing Clarifiers: These anaerobic solids do not settle well and no additional clarifier volume would guarantee settling. Further, producing a thicker solids stream (as a flotation thickener can produce), has additional process benefits such as increasing the hydraulic retention time in digesters, and reducing return pumping rates which allows more control over the operation and performance of the industrial digesters.
3 Pilot Testing Methods
The following is a summary of the pilot operation methods.
3.1 Set-Up
Each manufacturer set up their pilot unit in the northeast area of the industrial site. The influent to each unit was pumped from the existing entrance to the separators.
Chemicals and air were introduced to the pilots per the manufacturer recommendations with assistance from the City’s chemical supplier Chemsolv. The photos in Appendix B show the pilot set-ups.
3.2 Start-Up
The pilot test period was intended to be August 17, 2020 to August 28, 2020. Pilots were run during the weekday, daytime hours general from 7am to 3 pm.
- The SAF arrived to the site early and was operating prior to August 17th,
- The DAF arrived on Friday, August 14th and took longer to setup. The DAF was not operational until the Wednesday, August 19th, As a result, the DAF was operated two additional days of August 31st and September 1st, with the approval of the City and Plant Operators.
3.3 Testing
Process and water quality parameters were monitored and sampled in the wastewater influent and the effluent of the SAF/DAF pilot. SEH/City recorded parameters on a log sheet and took field measurements using provided instrumentation on a daily basis. Samples were collected for laboratory analyses for parameters that cannot be measured in the field and to check field results. All samples were grab samples (no composites were run). Samples were collected at similar times so they could be compared to each other. If a unit was not performing well, both samples were delayed until the unit was performing better.
A sample log was created to document the sampling and necessary tests. Some tests were conducted multiple times per day and others just a few times during the 2-week pilot. Table 1 summarizes the testing completed.
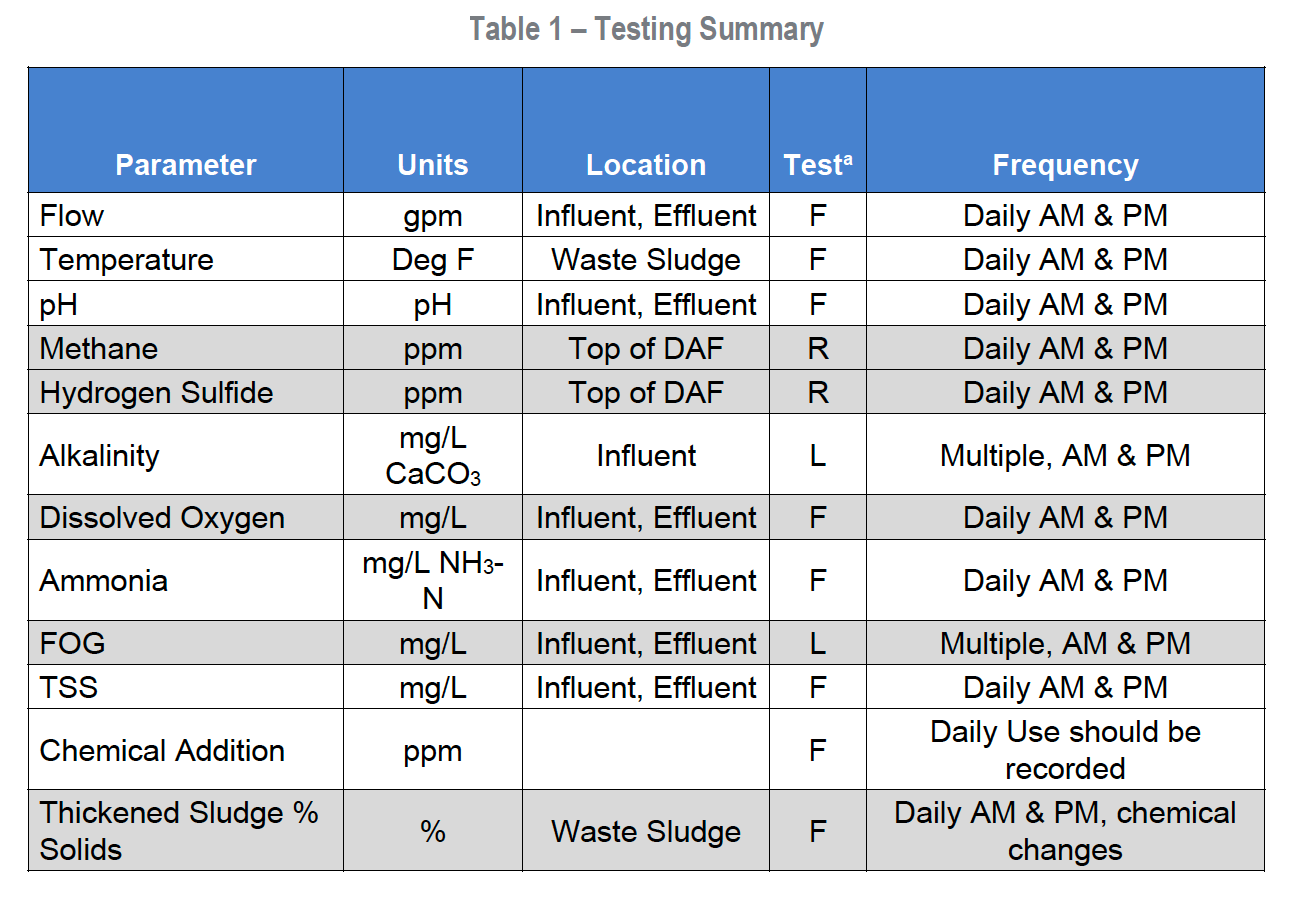
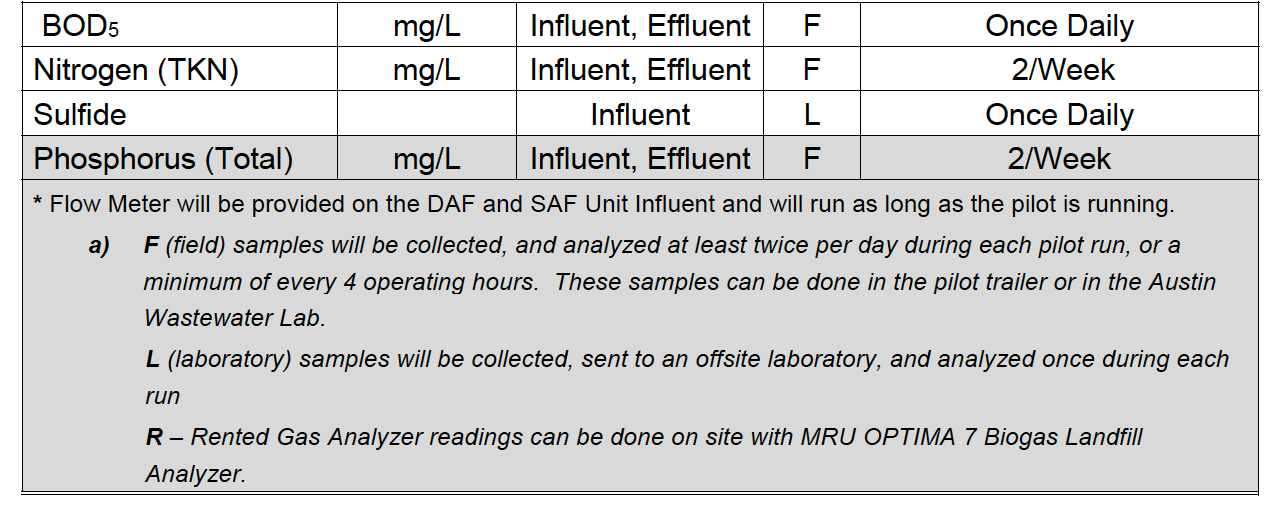
4 Pilot Testing Results
When comparing the results of the two pilots, there are several key criteria:
- Design Parameters: Piloting offers the opportunity to determine sizing to right-size the
- Performance: Data was collected to determine to overall performance of the two systems. This included TSS removal, thickened sludge capability, and contaminant
- Operational Conditions: One objective of the pilot testing was to understand design criteria and operational conditions.
4.1 Design Parameters
The pilot testing provided data to refine the design (and the associated costs) with respect to equipment sizing and chemical use. These design parameters are described below. Cost implications of the design parameters are incorporated into the costs presented in Section 5.
4.1.1 Solids Loading Rate
Original quotes for the flotation systems were based on the manufacturer’s best estimates of solids loading rates that the systems can handle. Solids loading rate is presented as the pounds of solids coming to the unit per hour per square foot of tank area (lb/sf/hr). The higher the assumed solids loading rate, the smaller the footprint required.
- SAF: The SAF operated fairly consistently at an influent flow rate of 150 gpm, though it was increased to 185 gpm to view the effect on The average solids loading rate was approximately 22 lb/sf/hr, with a high of 32 lbs/sf/hr without failure. The original quote from Heron assumed a loading rate of 14.6 lb/sf/hr. The SAF system size quoted did not change as a result of the pilot testing.
- The DAF operated at feed rate of approximately 100 gpm the first week. The lamella plates seemed to hinder the performance of the DAF, as the sludge blanket was too thick and was clogging up the lamella plates, decreasing efficiency overall and causing frequent failure of the DAF. On August 22nd, 2020 (Saturday) the lamella plates were removed, and the pilot was run the following week without these plates. Efficiency and failure rates were greatly decreased, and operational issues decreased also. Flow at this point was increased to 150-200 gpm, and eventually up to 300 gpm. At the end of the pilot, the solids loading rate was as high as 15 lb/sf/hr, with an average of 11.8 lbs/sf/hr. The original quote assumed a loading rate that was higher based upon the additional surface area of the lamella plates, and thus will be lower based on the results of this pilot. The DAF company has not provided an updated quote, though the price is expected to increase.
4.1.2 Chemical Requirements
The pilot testing provided the opportunity to determine the required chemical volumes. Appendix A includes the summary of the chemical usage.
- SAF: The SAF required 36 ppm polymer at a cost of $1.14 per pound in dry polymer; US 9115 from Chemsolv was used. As a result of the pilot testing, the estimated annual polymer costs increased by $149,000 from earlier estimates. The SAF also used surfactant, called Floc Aid A01W, supplied by This surfactant is estimated to cost
$125,000 per year. Heron stated that the price of the surfactant has not changed over time and they have multiple chemical companies they can use to mix this chemical blend.
- DAF: The DAF took a little while to dial in the chemical type. During the first week, Chemsolv US 9449 was used. Several different polymer blends were tried, and did not work. On August 26th the polymer was switched to Hawkins AquaHawk 1191 which worked the best and held the floc together. On average at optimum working conditions, the DAF used 60 ppm of The price of this in polymer in dry form was not able to be obtained at the time of this report, but was assumed the same as the Chemsolv US9115 (although it probably is more expensive). As a result of the pilot testing, the estimated annual polymer costs increased by approximately $416,800.
For both systems, the pilot testing resulted in a better understanding of the chemical demands, which were greater than originally estimated. Further refinement and optimization of the chemical costs is possible with the full-scale operation, but was not feasible with the duration of the pilot testing.
Additionally there is currently coagulant (Chemsolv US9080) that is added between the Anaerobic Digesters and the Aeration tank. The City currently adds this to improve settling in the clarifiers. On Friday August 28th, 2020, the coagulant was temporarily turned off to see what impact it had on the pilot units. Both pilots were able to operate at a similar TSS removal rates without the coagulant than with it. However, since coagulant operators on a micro level, and polymer operates on a macro level, smaller fine particles of TSS were noticed in the effluent compared to effluent without the coagulant. These additional fine particles however were not enough to influence the TSS removal efficiency as can be seen on the TSS values for this day. Barring other plant operational issues, we believe that the coagulant can be removed from future DAF/SAF operation.
4.2 Performance
The performance of the two pilot systems can be determined by comparing the TSS in effluent (percent of the total solids removed) as well as the degree of thickening obtained. Additionally, testing results were included for common parameters, such as phosphorus, total Kjeldahl Nitrogen (TKN), BOD5, ammonia (NH3), and pH.
4.2.1 TSS Performance
Table 2 summarizes the TSS performance. The SAF resulted in better TSS performance. Figure 1 presents the plot of the influent and effluent TSS concentrations. Typically DAF’s would provide between 90-99% solids removal. Both pilot units were able to achieve this on average, but the DAF did not achieve this at all times.
The DAF TSS performance is heavily influenced by three samples with high TSS (greater than 850 mg/L). Because of the way sampling was conducted, SEH believes that these high values are representative of the variation that the full-scale system might see resulting from system adjustments that are required as influent characteristics change. Sampling for the DAF did not start until Wednesday 8/19 of the pilot, which prior to this, the system was struggling with start- up/pilot challenges of getting all the equipment to work and finding the right polymer. Additionally, samples were generally not collected at times when the DAF pilot was temporarily not performing well.
The SAF had a two samples where the effluent TSS concentration was elevated, though not to the degree of the DAF (178 and 194 mg/L). Even with these higher concentrations, the SAF was still removing greater than 96% of the solids, which is well within the expected range for DAF systems.
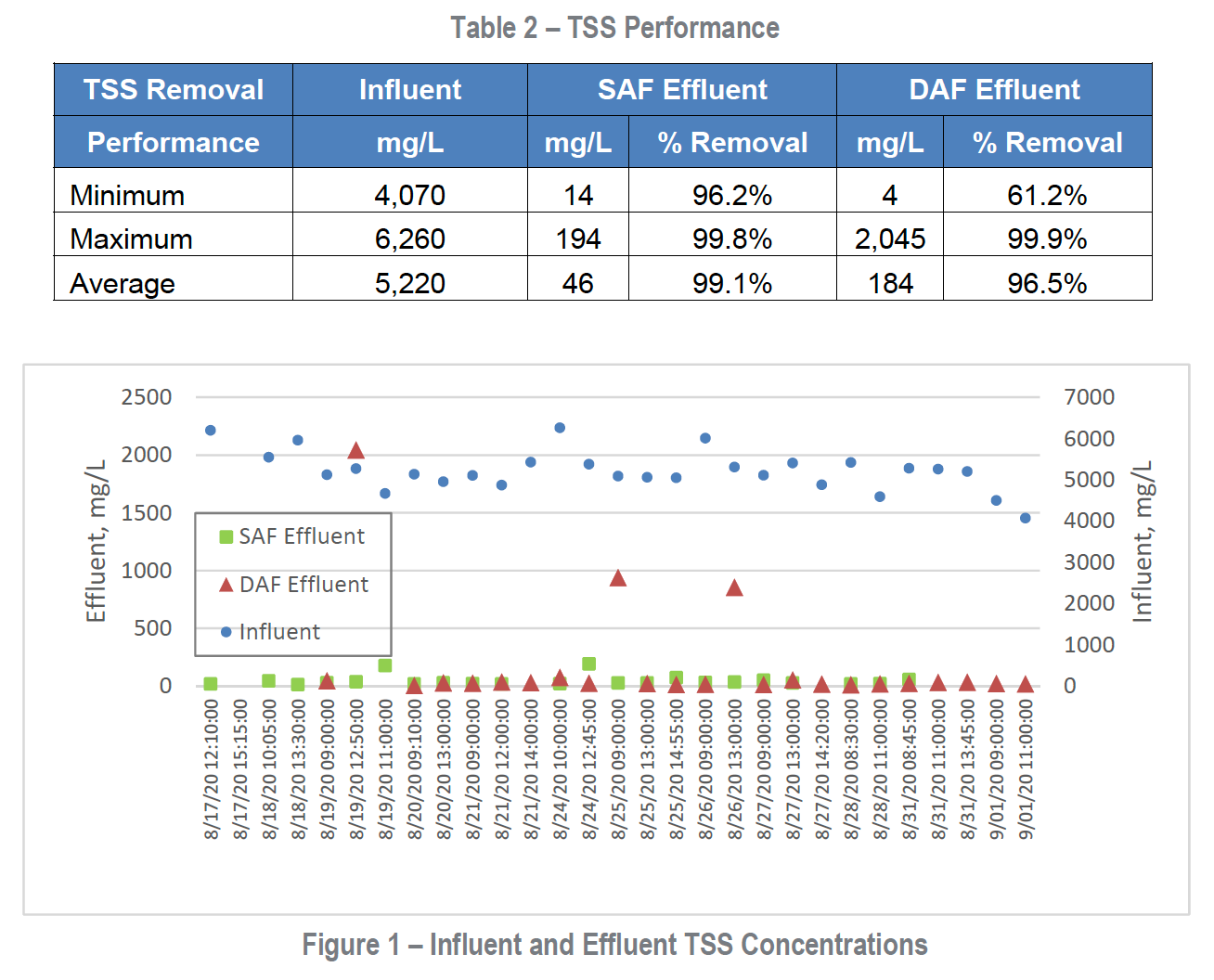
4.2.2 Thickened Sludge Performance
Another important performance measure for a separation system is the thickened solids concentration. The current separators achieve approximately 0.75 – 1% thickened solids. As a result, a large volume must be returned to the digesters to return the mass of solids required. The flotation technologies produce a thicker solids product, which means a much smaller volume of solids (though the same mass) returns to the digesters. This offers a number of benefits, including reduced pumping costs and improved treatment performance by having better control over the solids retention time (SRT) in the digesters.
Table 3 compares the thickening performance of the two pilot units. The two units performed equally well in this regard.
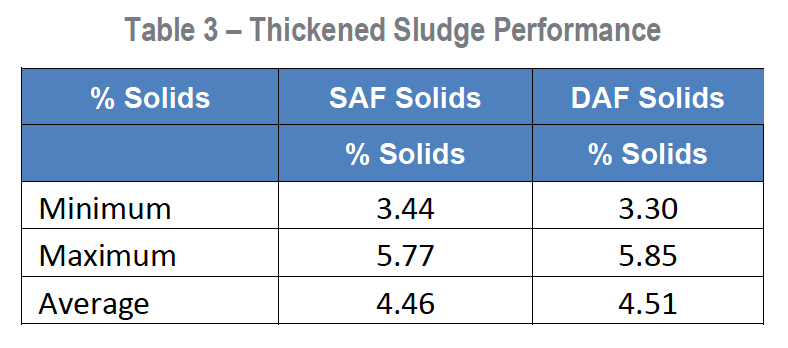
4.2.3 Other Performance Factors
Other parameters were monitored to see if there were differences between the technologies, but also to help characterize the anticipated effluent from the separator technology for considering the design of downstream processes. Table 4 summarizes the results of these other parameters. Generally, the two systems performed very similarly with respect to these additional parameters. The SAF had effluent quality that was marginally better, but as it relates to operation and design, the difference is not relevant.
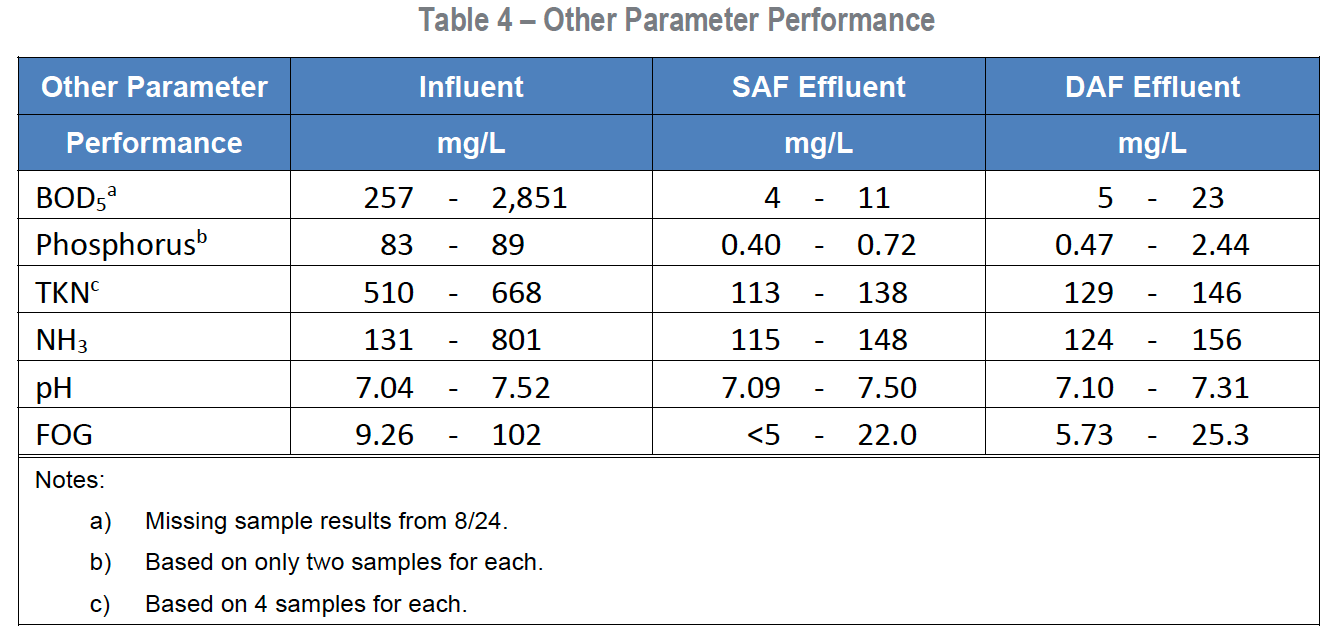
4.3 Operational Conditions
One of the other objectives of the pilot testing was to determine if there were any operational considerations that needed to be factored into the design or the selection of the system. The operational conditions are summarized below.
4.3.1 Hydrogen Sulfide
SEH had concerns related to the off-gassing of the effluent, which would contain hydrogen sulfide (H2S). Hydrogen sulfide can cause deterioration of interior components if not handled properly. The air space above each pilot was tested for H2S. The measured H2S was between 0 and 1 ppm for both pilots. This is quite low compared to the biogas measured at up to 1,000 ppm H2S in the past. H2S has an air odor threshold of 0.008 to 0.13 ppm. So while there is not concern over deterioration, especially in a well-ventilated room, there will still be some odor coming off the DAF/SAF (not unlike the separators today).
4.3.2 Methane
Methane gas when combined with oxygen can result in a combustible gas mixture. Methane concentrations between 5% and 17% will support ignition. SEH wanted to verify that the off- gassing resulting from the air addition in the flotation systems would not create a dangerous atmosphere. Methane levels were well below the lower explosive limit with a peak recorded methane level of 0.22% in the airspace above the pilots.
4.3.3 Dissolved Oxygen
SEH also had some concern about the addition of dissolved oxygen (DO) and the introduction of this oxygen to the anaerobic digesters through the return solids. The influent DO coming from the industrial aeration tank was only 0.18 mg/L on average. The flotation pilots added DO to the effluent for concentrations of approximately 2 mg/L. This is relatively low DO and it is expected to get consumed in the piping and pumping systems before making its way back to the Anaerobic Digesters.
4.3.4 Pilot Operational Observations
Pilot testing also afforded the opportunity for the plant staff to operate the systems. Table 5 summarizes some of the operational observations from the pilot testing. Generally, the SAF pilot operated without issues. The DAF was sensitive to the increased loadings that occur on Mondays and needed more frequent adjustment. After piloting the two units for two weeks, there was consensus among the operations staff that the SAF system was easier to operate and more reliable.
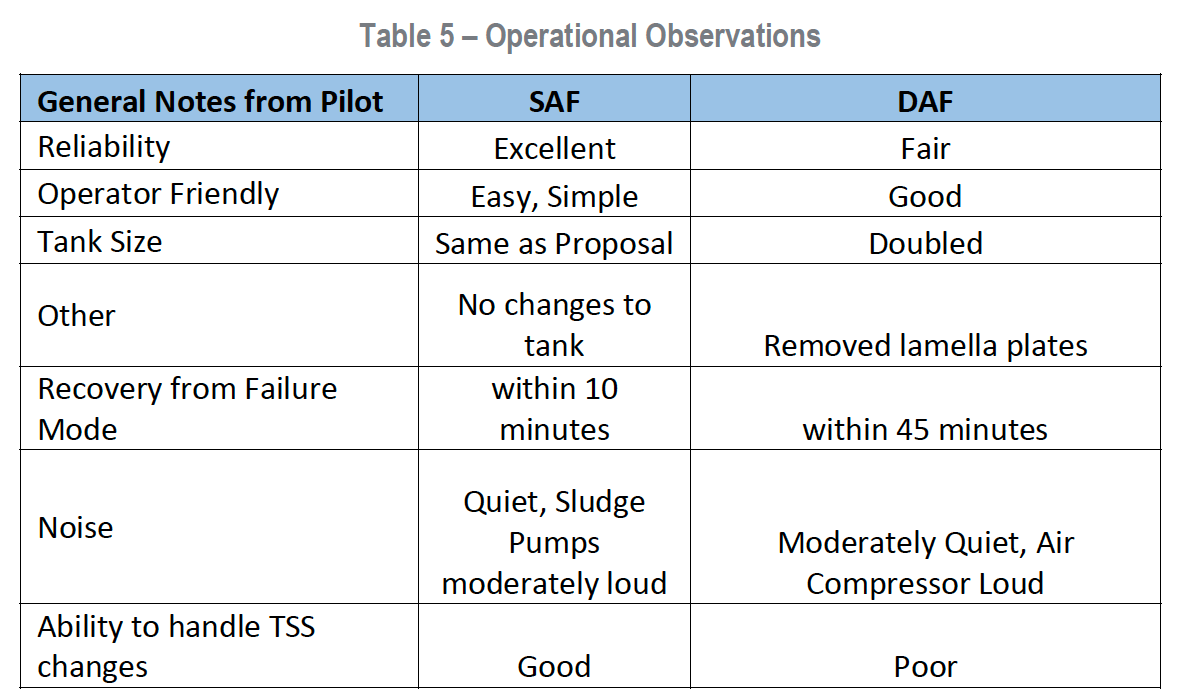
5 Costs
Based on the pilot results, the cost estimates for the SAF and DAF have been updated. However, the DAF company did not provide an updated quote, though were aware of the urgency to finalize the selection. The DAF company knew that they needed to sharpen their pencil to compete with the SAF, and it seems they have not landed on a cost that they are comfortable quoting at this time. Costs are updated to reflect the known chemical quantities and the estimated additional footprint for the DAF, and 25% estimate added to the equipment cost for the DAF.
Based on the updated costs, the SAF has the lowest capital and present worth cost.
6 Recommendations
SEH recommends the suspended air flotation technology for industrial separation based on both monetary and non-monetary considerations. This technology has the lowest capital cost of the technologies considered. The annual operations costs were higher than originally estimated (for both the SAF and DAF). It is likely that other separation technologies would also have higher chemical demands. The SAF offered greater treatment consistency and reliability when compared to the DAF.
Download The SEH Study
Fill out the form to download the full study including raw data, dosages, results, and price comparison, as presented by SEH.